Make Your Own Mould & Deckle
I’ve been making paper for many years and I have to say that my absolute favorite mould is made by Timothy Moore. I’m not sure that he is even taking orders for moulds anymore (and if he is, he has a pretty long waiting list). Tim’s moulds are very expensive, which is totally worth it if you are a professional papermaker, but not so much if you aren’t as serious about the craft.
I have also purchased a new wove mould from Chester Creek Press. Robert Walp is making high quality moulds and deckles. Fair warning: good tools are high priced, but they are definitely worth it if you’re in the business of making paper.
Stephanie Hare also makes beautiful moulds and deckles for making stationery. These are high quality for what they are – plastic screening, finely sanded and slick surfaces and cool magnetic connectors to hold the mould and deckle together when sheet forming.
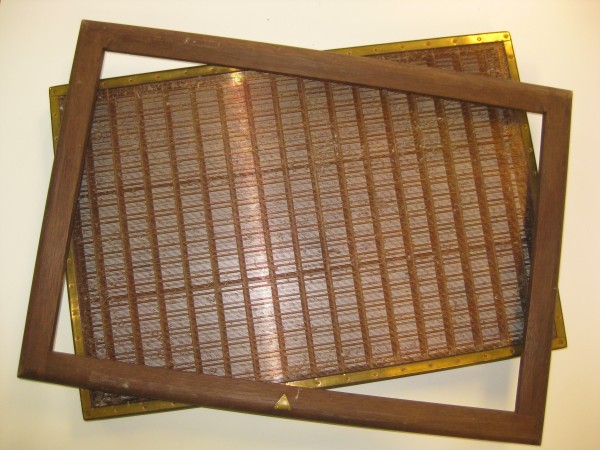
My 12″ x 18″ professional mahogany mould made by Timothy Moore
There are a few papermaking suppliers that carry moulds and deckles, too: Carriage House Paper, Twinrocker, and Arnold Grummer are the suppliers that I’m familiar with.
But it isn’t that complicated to make your own mould and deckle. Below are instructions excerpted from my book, The Papermaker’s Companion…
I made the following mould and deckle with needlepoint stretchers that were already jointed. You can find these at craft stores like Michael’s, or if you need quantities in bulk, try Marie Products. If you have basic carpentry skills, you can purchase lengths of 1-inch-by-1-inch pine (or more expensive hardwoods) and joint them yourself.
Here are the supplies you will need to make a mould and deckle that will form a sheet of 81⁄2″ x 11″ paper.
4 prejointed needlepoint stretcher bars measuring 10″ x 3⁄4″ x 3⁄4″
4 prejointed needlepoint stretcher bars measuring 121⁄2″ x3⁄4″ x3⁄4″
Water- and weather-resistant wood glue
Drill and drill bit
Eight 1⁄2″ brass or stainless-steel screws
Sandpaper
Small paintbrush
Water-based polyurethane (oil-based is also okay, but I don’t like the fumes)
Tin snips for cutting wire
Rustproof wire screen (window screen or finer), cut to 91⁄2″ x 12″ (24 x 30 cm)
Hardware cloth (a heavy wire mesh with 1⁄4″ mesh squares) cut to 91⁄2″ x 12″ (24 x 30 cm)
Rustproof staples and staple gun
Duct tape
Scissors
1⁄4″ or 1⁄2″ foam insulating strips (aka weather stripping)
* Note: Marine supply stores are a good source of waterproof and rustproof items, such as paints, staples, and screws

Illustration by Alison Kolesar from The Papermaker’s Companion
- Apply carpenter’s glue to the joints and fit them together to form two wooden frames. Make sure the corners are square. Drill holes in the corners and fit with screws to secure the joints. Sand the surfaces to make them smooth and even.
- Apply polyurethane with a brush to waterproof the frames and let them dry at least overnight. I recommend applying a second coat.

Illustration by Alison Kolesar from The Papermaker’s Companion. The hardware cloth doesn’t appear in this illustration, but it is a helpful addition!
- To make the mould, place the window screen on top of the hardware cloth and lay the combined screen onto one of the frames. Center it and staple it to the frame at 1-inch (2.5 cm) intervals, keeping it taut. Put duct tape over the stapled edges to seal the screens and prevent pulp fibers from slipping between them. This also protects your hands from the sharp edges of the screens.
* Note: There are alternatives to wire screening. Carriage House Paper carries a heat-shrinking polypropylene screening that can be glued to the frame and tightened with the heat of a blow dryer.

Illustration by Alison Kolesar from The Papermaker’s Companion
- To make the deckle, cut the foam strips to fit along the inside edge of the “window” on the other frame. Use a staple gun to attach the foam strips at 1-inch (2.5 cm) intervals.

Illustration by Alison Kolesar from The Papermaker’s Companion
*Note: Your mould and deckle will wear over time, and the wire mesh may sag. This is why professional equipment has an extensive ribbing system. You can support your mould and deckle by cutting a rabbet groove on the pine lengths of the mould and sliding a piece of plastic grid (the kind used in fluorescent lighting) into it before you attach the screens. When using this type of mould, make sure you clean it well by spraying from the front with water, because pulp tends to get caught between the screen and grid.
And here’s an extra tip, which I tried out just today! If your papermaking screens do get clogged with pulp (my water pressure isn’t great, plus I’m working in a studio with no floor drain) soak them in water for a few hours and then take them to the manual car wash. Use the pressure sprayer to blast the excess pulp off of your screens.
Happy mould making!
I’d love to hear about the types of moulds & deckles that you use! Feel free to leave a comment and share your experiences!
10 Comments
Magnolia Editions in Oakland is working on plans to make molds and deckles as well as su-gettas on a 3D printer, although I don’t know how heavy they will be using 3D resin. They are also considering plans to cut wood on a laser cutter to assemble into molds.
I made my first set of molds and deckles out of wood from an IKEA shoerack I picked out the trash! Still have them, still work!
This is very cool, Michelle. Brian Queen has explored this as well, but I think it is still fairly costly. I don’t love the plastic screens (prefer wire mesh) and I don’t know of a supplier who carries that type.
Hi Michelle and Helen,
We’ve used the lighting ‘egg crate’ for the screen support on AG dip and pour handmolds from the start. We provide a loose (non-secured) paper making screen which is stiff enough to handle after sheet-forming, and helps with the issue of pulp gathering between screen and grid. Love the car wash power hose concept! We never met a screen we couldn’t clean, but clogging can certainly be an issue.
Thanks for the post and remarks!
Kim
I have experience as a painter. I would like to give some advice on stretching, if you plan on using screen material other than metal mesh.
When stapling to the screen.
First place the mesh on the table and set the frame on top. Choose the center of one side and loosely pull the material over and staple onto the back, so as to not move to much of the material.
Next staple the opposite side at center. This time you should pull harder so that you see a line of tension.
Now staple the center of the other two sides. The first should be pulled gently and the other more firmly. The four staples should be tight enough that you now see tension lines that create a diamond shape.
From this point, you wil work from center out to the corners. Choose a direction left or right. Say I choose to staple from center to right. The first side should be pulled gently. While you do this, you should the pull the material slightly toward the right, to get the bunchiness out.
Staple that side. Turn the frame 90 degrees and staple From center out to the right. Do this on all four sides from center to right.
After this is done, you can start stapling from center and to the left on all sides. Make sure to be more firm in tensioning and you should get even tension throughout the mesh.
Hope that helps.
Ian Epps
Kim,
visited your website to understand the “loose (non secured)” concept, and I like it, especially those velcro strips on the tall deckle to keep the whole thing together (I wasn’t too happy with elastic shock cords)
http://arnoldgrummer.com/media/catalog/product/cache/1/image/9df78eab33525d08d6e5fb8d27136e95/a/g/ago301dvd.jpg
might solve my issue, having just laser-cut a nice “laid screen” pattern on some very thin plastic – it is fragile, so I was worried about washing it later, etc. Making it removable solves a few things.
Ian,
enormously appreciative. I have been rescuing former silk-screen frames, but my tensioning was pitiful. Now it will improve 🙂
I have noticed that your page needs some fresh content.
Writing manually takes a lot of time, but there is tool for this boring task, search
for: unlimited content Wrastain’s tools
When I made mould/deckles for my wife, I used 1/4-inch hardware cloth (aka galvanized metal mesh) under the brass screen as a support. Works pretty well to prevent sagging, though as she uses Himalayan (deep) deckles, the issue of pulp collecting underneath doesn’t happen.
Would someone answer my question please. I wonder if any type of duct tape will work, there seems to be several kinds and I don’t think they are all created equal.
I use standard duct tape with string in it, like this: https://www.amazon.com/Duct-Tape-Professional-Residue-Weather/dp/B07G2TB7W7/ref=asc_df_B07G2TB7W7/?tag=hyprod-20&linkCode=df0&hvadid=507720025611&hvpos=&hvnetw=g&hvrand=3235616384546142025&hvpone=&hvptwo=&hvqmt=&hvdev=c&hvdvcmdl=&hvlocint=&hvlocphy=1014497&hvtargid=pla-1245340293549&psc=1
Yeah….I’m on a budget. I used an old thinly slotted bamboo placemats and from a door screen someone threw out at the apt garbage can. Also, someone moved and put a wood bedframe next to the dumpster, so I took it. Started to saw it by hand…Stopped. Took it to Lowes and asked nicely and the guy cut it down for free. and told me which screws to get for my drill. I think the maintenance people think I’m crazy now lol ….can’t help being so drawn to it…..