How do you Press?
I was in Salt Lake City this past weekend, teaching an Experimental Papermaking workshop at the University of Utah. They had this really cool press! You could raise and lower that top bar to accommodate varying post sizes. And check out that cute little jack. This press worked really well for our 8″ x 10″ sheets of paper.
Often when I’m teaching, the question arises about how to press papers in a home studio. Here’s a bit about pressing (with some added bits) excerpted from my book, The Papermaker’s Companion. Illustrations in this post are by Alison Kolesar from the book.
Pressing removes water from the sheets of paper and compacts the fibers tightly together as they bond. After pressing, the sheets will still be damp and will need to be dried. All kinds of systems have been rigged for pressing, ranging from piling heavy books or rocks onto the post to using a garbage bucket filled with water (the more water, the more weight) and using a hydraulic jack to create pressure. The first presses in Europe were wooden screw presses, which took the strength of many men to tighten. Similar presses were used in the Far East.
In some countries, papermakers developed systems of drying sheets of paper directly on the moulds, eliminating the need for a press. Other systems involved drying sheets on boards or walls. Some of the techniques described here are centuries old, while others are recent innovations, developed by contemporary papermakers who have designed systems to meet their needs. Several papermaking suppliers sell presses.
Sponge Press
A low-tech method of pressing is using a sponge — use a clean sponge, so that you do not contaminate your paper. To do so, press your sheets individually as you make them and then hang them on a line or place them in a rack. I recommend that you couch onto pellon when you press with a sponge, because it is less absorbent and will require less sponging. Take one sheet of paper with its pellon and place it onto a dry felt or newspaper (something that will absorb some of the water). Then place a dry pellon on top of the sheet to protect the sheet’s surface, and gently but firmly sponge water out of the sheet. Repeatedly wring out your sponge and continue pressing the rest of the sheet. Be careful not to damage the sheet by pressing too hard; still, remove as much water from the sheet as you can. It is also important to press the sheet evenly, so that all of it will dry at the same rate. Your sheet is now ready to be dried (see my blog post about drying). Continue pressing the remaining sheets.
➤Instead of a sponge, you can use a rolling pin or an ink brayer to remove moisture from your sheets. Since these tools do not suck up moisture like the sponge, you will need to place your sheet in between something absorbent, like newspaper, towels, or felts, so that the moisture is transferred to the absorbent material as it is rolled out. Press gently at first — if you press too hard, you will distort your sheet.
Found or Adapted Presses
You might adapt or use a press that was designed for another use, such as a flower press, cider press, or book press. Just make sure you can fit a stack of paper into it (many printing presses press only one sheet at a time), and watch out for presses with metal parts that will rust. The staff of the Dieu Donné Papermill, a hand papermill in New York City, for instance, needed an electrically powered hydraulic machine that could press up to 100 sheets of paper. They found the perfect machine, a farm implement originally designed to bale hay. It can press over 100 sheets at a time.
Pressing Multiple Sheets
Note: If you are pressing different types or sizes of papers together, you might want to put a barrier of wood, metal, or firm plastic between the layers, so that they are in effect pressed separately. For example, if you are pressing plain white sheets together with pigmented sheets of paper, they should be separated by a barrier so that the color does not bleed into the white sheets. In this particular case, the white sheets should be on top of the barrier to ensure that no color drips down onto them.
Hydraulic Presses
Many papermakers have built presses that uses a car jack for pressure. I have seen many variations of this press at facilities around the country, each constructed to meet the pressing needs of a particular studio.
Arnold Grummer has a nice portable press for use in the classroom.
Making Your Own Simple Press
A step up from the sponge press is a simple plywood press. Your post of paper can be placed between two polyurethaned boards (or two plastic cutting boards), and C-clamps can be attached to each of the four corners and tightened. Pressing will release a fair amount of water, so you might want to work over a tub or tray, or work outside.
A similar plywood press is easy to build, and I’ll post instructions for building the press pictured below soon.
Vacuum Table Press
During the 1970s, papermaking made a resurgence as an art medium in America. Artists began “pushing the medium,” developing innovative ways to work with paper and pulp. One such innovation is the vacuum table: a tabletop with small holes in its surface, a holding tank underneath, and a connection for a strong wet-dry vacuum. Plastic is draped over sheets of paper lying on the table surface, and when the vacuum is attached and turned on, it sucks the plastic down onto the sheet, drawing water out. This system can press very large sheets of paper — which would be difficult, if not impossible, to fit into a hydraulic press (not to mention lifting them into it) — as well as high- and low-relief sheets and sculptures. Instructions for building one such vacuum system can be found in Volume Six, Number One of Hand Papermaking magazine. Some papermaking suppliers also carry them.
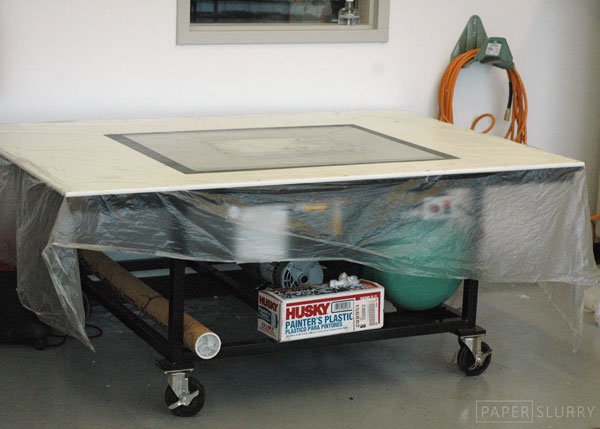
Vacuum table at Longwood University
Using a Hydraulic Press
Many papermakers use hydraulic jacks to supply the force in their press. When you’re using any type of hydraulic press (press with a hydraulic jack), load your post of paper into the open press, then bring the press to full pressure. In some cases — for example, if your paper is very thick — you might need to press the paper gradually. This is very important, because if you press too quickly, the water will explode out and damage the wet paper. When the press has been brought to full pressure, leave it for 15 minutes to an hour, depending on your press and the particular post of paper. You want to make sure that water is removed from the entire sheet. With most presses, the pressure hits the center of the sheet first, and allowing it to sit gives the water time to move from the center and seep out of the edges. Release the tension and remove the post when you are done. If the sheets still seem very wet, you can press them again. The sheets are now damp and ready for drying. Although it is not necessary, fitting a hydraulic press with a gauge that measures the pressure can be handy, enabling you to record the amount of pressure you use for different techniques. In general, you can press papers to full pressure, but if you are board or loft drying, you will need to adjust the amount of pressure you apply.
14 Comments
Great article, Helen. Good info, easy to understand. Photos & drawings are most helpful. Thanks for the inspiration.
Dear Helen,
you´ve always interesting and well written and
photographed articles about paper and many more.
Thank you very much therefore.
This “pressing” article is one of my favourites 🙂
Yours
Sabine from Germany
In a class that I took with Nance O’Banion she stretched silk screen “silk” material on a wooden frame, placed the wet paper couched on Pelion and dried it from the back with a wet dry vacuum. I used this process for many years and it worked fine. My frame was originally made of stretcher bars for stretching canvas but then I built a big frame.
Hi Roslyn! Yes, this is a fabulous way to press and dry papers (I mention it in the drying section of my book). They have that type of screen set up at Penland. thanks for mentioning it!
Thanks for all the information. My husband built my first press (screw type with a frame made from enamelled metal pipe) and it has worked well, but there is a jack sitting in my studio waiting for the next iteration. Your pictures will help with the design.
And although I live in the countryside and see bailers regularly, it would never have occurred to me to use the packing part of one as a paper press: very clever!
What’s up to every one, the contents present at this website are in fact
amazing for people knowledge, well, keep
up the good work fellows.
Thanks. I’m wondering if you have any sources for plans for building a small hydraulic press? I found plans once before on the internet, but a recent web search didn’t come up with anything. Best, David.
Dear Hellen,
I’m at the very beginning of my paper making journey, so I have few doubts. One of those is, how much pressure is needed to press the paper sheet?
Thank you!
[…] for the latest electronic gadget, we artists and entrepreneurs are nursing a buzz from new ideas, new art supplies, and new inspiration. It would be foreign to live any other […]
HI! A jack paper press can be found at:
https://affordablebindingequipment.com/hydraulic-jack-papermaking-press/
and a hand crank press can be found at:
https://affordablebindingequipment.com/paper-making-press/
Also available is a drying box:
https://affordablebindingequipment.com/papermaking-drying-box/
and a complete line of bookbinding equipment.
How can I emboss a paper with a press?
For those who might be interested, a press similar to the first press shown is now available at:
https://affordablebindingequipment.com/hydraulic-jack-papermaking-press/
Dear Helen, All,
I’m a newcomer to papermaking and started and have a metal paper/book press that I am using. In a happy accident, I forgot to put a felt over the top sheet so it stuck to the metal. When I found it the next day, now dry, the part of the paper
in contact was the most beautifully smooth, almost store quality surface. Do you, or anybody on this page, have experience using metal sheets to further flatten the paper (after the initial press) to replicate this smoothness?
With thanks, Rob
Rob, I have pressed or brushed paper onto glass, plastic and metal sheeting. It has to be done one at a time, which is another step in the process, but you’re right, you get a really smooth sheet. In commercial papermaking, there’s hot press paper – that is actually run through a very strong press to calendar/smooth out the sheet.